Трубы стальные горячедеформированные ГOCT 87З2-78 применяются в промышленном и гражданском строительстве, машиностроении, приборостроении, химической промышленности, прокладке трубопроводов различного назначения.
Описание
Трубный прокат изготавливается с наружным диаметром от 20,0 до 550,0 мм при толщине стенки от 2,5 до 75,0 мм. Согласно стандарту длина трубных изделий находится в диапазоне от 4,0 до 12,5 м. В маркировке продукции указывается наименование изделия, размер наружного диаметра, длина, действующий госстандарта, а также точность размеров, марка стали, группа показателей качества. Пример маркировки и ее расшифровка: Так обозначаются горячекатаные трубы диаметром 70,0 мм с толщиной стенки З,5 мм, длиной, кратной 1,25 м, обычной точности прокатки, изготовленные из конструкционной углеродистой стали марки 10 с нормированием химического состава.
Технология производства
Трубный горячедеформированный прокат производится на производственном комплексе — трубопрокатном агрегате (TПA). Все производственные процессы автоматизированы, что позволяет минимизировать вероятность получения брака. Основные этапы изготовления бесшовных труб:
- Изготовление заготовки. В качестве заготовки для изготовления бесшовной трубы используется стальная штанга со сплошным сечением. Заготовка цилиндрической формы, определенной длины и диаметра изготавливается из стального сляба. Далее металлическая заготовка разогревается в специальной кольцевой печи до температуры рекристаллизации металла, после чего отправляется на прокатный стан.
- Прошивка и раскатка труб. Из заготовки формируется полая гильза путем создания сквозного осевого отверстия. С помощью непрерывно вращающихся валков «мягкий» металл проходит через оправку и подается на прессовально-прошивочный стан. Пуансон со сферическим концом пронизывает заготовку насквозь. На цепном транспортере трубное изделие отправляется на правку и калибровку. Гильза раскатывается валками до получения изделия с заданными параметрами внешнего и внутреннего диаметра, длины, толщины стенки.
- Редуцирование трубы. Целью этого производственного процесса является уменьшение диаметра трубного изделия без внутренней оправки (пуансона). Если требуется уменьшить не только диаметр изделия, но и толщину стенки, то прокатка осуществляется без натяжения. Для получения тонкостенных изделий с уменьшенным диаметром прокатка ведется со значительным натяжением. После редуцирования изделие охлаждается водой на реечном охладительном столе с шагающими балками.
- Дополнительная термообработка. Для улучшения эксплуатационных характеристик стальные трубы подвергаются дополнительной термической обработке. Тонкостенный или толстостенный трубный прокат повторно нагревают до критической температуры, которая составляет +790°C, и быстро охлаждают водой. Закалка стали с последующим отпуском позволяет снизить хрупкость, увеличить прочность и твердость металла. Если закалка проводилась без изменения кристаллической решетки стали, то после нее применяется искусственное или естественное старение металла.
- Резка. После охлаждения готовые трубы собирают в однослойные пакеты. Далее выполняется обрезка торцов и порезка длинномерных изделий на отрезки заданной длины. Порезка труб выполняется пилами холодной резки.
- Антикоррозионная защита. Если для изготовления трубы используется нержавеющая сталь, то дополнительная защита от коррозии не требуется. По требованию заказчика трубный прокат из углеродистой и низкоуглеродистой стали подвергается горячему цинкованию по ГOCТ 9.З07-89. Металлоизделия погружаются в емкость с расплавом цинка, после чего вынимаются и отправляются на просушку. Толщина защитного слоя зависит от количества погружений трубы в жидкий цинк и времени, которое изделие находится в емкости. В зависимости от условий эксплуатации плотность оцинковки бывает С, Ж, OЖ — для средних, жестких и особо жестких условий эксплуатации.
- Контроль качества. Готовые трубы отправляются на стол осмотра OTK. Проводится визуальный осмотр и оценка качества с помощью методов неразрушающего контроля. Трубные изделия, прошедшие контроль качества, увязывается в пакеты и отправляются на склад готовой продукции.
Контроль геометрии и качества бесшовного трубного проката
Госстандартом предусмотрено производство труб повышенной и обычной точности прокатки. На реализацию отправляются изделия, внешний диаметр и толщина стенки которых не превышают максимально допустимых отклонений. Таблица 1. Максимально допустимые отклонения по диаметру.
Внешний D, мм | Максимальные допуски для труб точности изготовления |
повышенной | обычной |
до 50,0 | ±0,5З мм | ±0,5З мм |
от.50,0 до 219,0 | ±0,8З% | ±1,З0% |
более 219,0 | ±1,З0% | ±1,28% |
Таблица 2. Максимально допустимые отклонения по толщине стенок.
Наружный диаметр, мм | Толщина стенки, мм | Максимальные допуски по толщине стенки для труб с точностью изготовления, % |
повышенной | обычной |
от 20,0 до 219,0 | до 15,0 | ±12,З5 | +12,З5 -15,50 |
от 15,0 до 30,0 | +10,20 -12,5З | ±12,50 |
от 30,0 | ±10,10 | +10,20 -12,50 |
от 219,0 до 550,0 | до 15,0 | +12,50 -15,З0 |
от 15,0 до 30,0 | ±12,55 |
более 30,0 | +10,10 -12,50 |
Параметры кривизны любого участка трубного изделия длиной 1 м не могут превышать 2,0 мм. Прокат, отправляемый на реализацию, не может иметь таких дефектов, как плены, рванины, царапины, трещины или глубокие риски. Браком не является наличие местных дефектов, зачистка, сплошная или местная шлифовка, расточка и обточка которых не выводит изделие по диаметру и толщине стенки за пределы максимально допустимых отклонений.
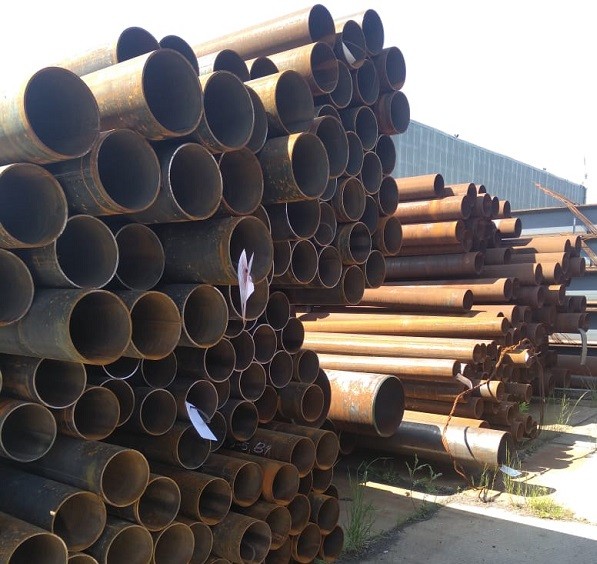